予測誤差
予測精度の向上も重要だが、どのような予測であっても、予測誤差は絶対に避けることができない。だからこそ、未来は予測できない前提で考えることが重要である。
予測はあたらない、だから欠品は起こる、そこで重要なポイントは、予測が外れた場合にいかに即座に計画変更ができるか、欠品があったときにいかにリカバリーできるか、という点に尽きるのではないだろうか?
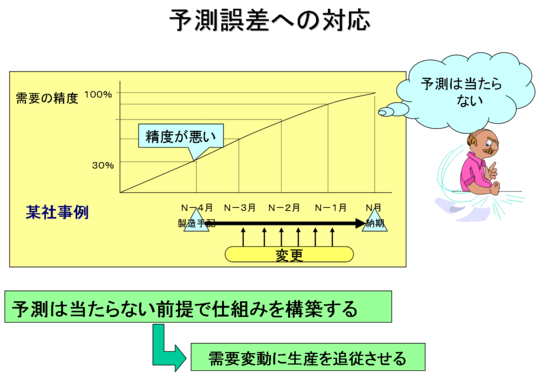
ある製品の事例でも、納期の4ヶ月前には製品仕様・数量のレベルで30%程度しか精度がなく、納期の1ヶ月前でようやく精度が90%になるものがあった。
この製品の製造リードタイムが4ヶ月だからといって4ヶ月前に生産確定してしまうと、その後の変更で、生産途中での変更が多く発生し、工程を混乱させるだけでなく、在庫も増大してしまう。
ことによると短納期で受注したときに類似品の在庫があるので、最初から製造するよりも、製品在庫を生産仕掛に戻し入れて、改造した方がリードタイ上も在庫削減の意味でも、良いということになる。
極端なケースでは、改造が常態化して、工場内に改造専用ラインまでできてしまうケースもあった。
だが、よく考えてみるとこれはおかしなことで、在庫もなくて、改造もしない方が良いに決まっている。これを実現するには、需要変動に生産を追従させる「仕組み」が必要なのであって、その結果、変化に強い会社・生産体制ができる。
実は在庫が少ないということは、会社のキャシュフローだけの問題ではない。製品在庫や中間品の在庫が多い状態で、新機種を開発し売りだせば、旧タイプの製品を営業は売る意欲を無くし、また、販売価格を下げてもなお売れなくなる。
さらに、営業のしらないところで、工場内では中間品の在庫がデッドストックになってしまう。工場では、変更のなく、生産数も安定した生産を望んでいるが、もはやそのようなことが許される市場ではないし、工場が営業に無理にそれを強いれば、結局のところ、製品の競争力を失って、工場で生産するものがなくなる事態に陥るのである。
市場の変化が激しいのは、1企業で変えることのできない制約条件であり、それに対応できる生産体制にしない限り、企業全体が生き残っていけない。
もしくは、変更の少ない製品であれば日本国内よりも中国生産の方がコストメリットがあり、国内で工場を維持する意味はない。
このように変化に対応できる工場でないと、生き残っていけない環境になっていることを再認識すべきだ。つまり、在庫削減はキャシュフローという経営課題であると同時に、結果として、国内の工場の生き残りをかけた取り組みとことを意味している。